The new energy revolution is triggering profound changes in the automotive supply chain
-
2024-08-22
-
Intelligent Manufacturing
Introduction: Amid the wave of the new energy vehicle (NEV) revolution, the supply chain is undergoing unprecedented transformation. This article delves into the core issues of this transformation, including challenges and innovations in the battery supply chain, the deep application of digital technologies, sustainable practices, and future trends in supply chain development.
One of the most compelling aspects of the article is the analysis of battery recycling and secondary use. With over one million tons of retired power batteries expected to require processing globally by 2025, the industry's focus has shifted to how this challenge can be turned into an opportunity. Through advanced technologies, over 95% of key metals can be recovered, not only reducing costs but also minimizing environmental impact. Additionally, the article explores the application of AI in demand forecasting, the role of blockchain in enhancing supply chain transparency, and how the "localized globalization" strategy is reshaping supply networks. These insights provide valuable decision-making references for industry professionals.
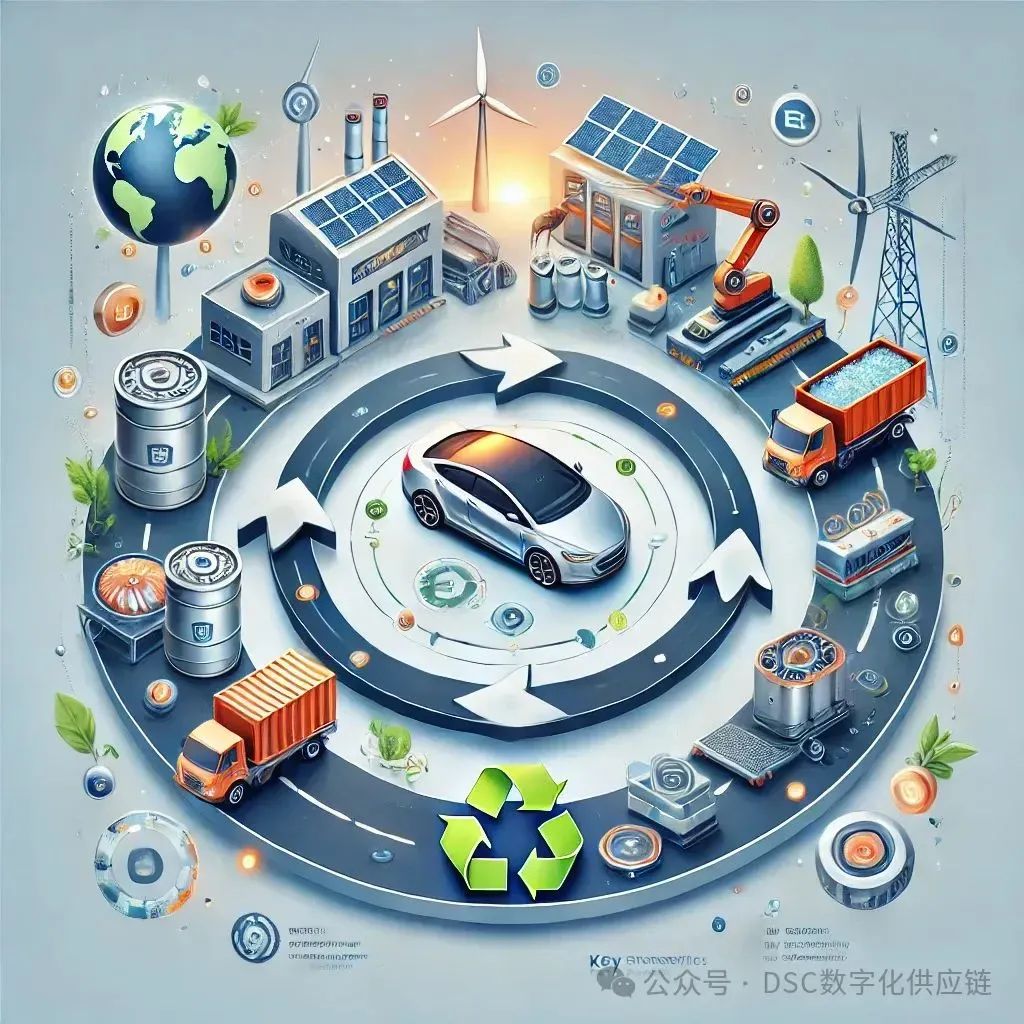
Amid the global backdrop of climate change, new energy vehicles (NEVs) are transforming the automotive industry at an unprecedented pace. In 2023, global NEV sales reached approximately 14.653 million units, marking a 35.4% year-on-year growth. The Chinese market, in particular, stands out, with NEV penetration exceeding 50%. This powerful wave is not only impacting traditional automakers but is also profoundly reshaping the entire automotive supply chain.
Traditional automotive giants are accelerating their transition to electrification. Companies like Volkswagen, General Motors, and Toyota have announced ambitious electrification plans, investing hundreds of billions of dollars in the development of new energy models and capacity building. Meanwhile, emerging Chinese automakers are sweeping the globe. The automotive industry is undergoing a transformation unlike anything seen in a century. The new energy revolution is not only changing the power systems of vehicles but is also completely reshaping the entire supply chain landscape. This transformation is as profound as the shift from horse-drawn carriages to automobiles in the early 20th century.
The most notable change is the shift in core components. Traditional internal combustion engine vehicles have about 30,000 parts, while pure electric vehicles require fewer than 10,000. This means that many traditional parts suppliers are facing the pressure of either transforming or being phased out. At the same time, new components such as batteries, motors, and electronic control systems are rapidly emerging as the new focus of the supply chain.
The importance of the battery supply chain cannot be overstated. As the most critical and expensive component of NEVs, power batteries account for 30% to 40% of the total vehicle cost. Therefore, ensuring a safe, stable, high-quality, and competitive battery supply has become the top priority for major automakers. We see companies from Tesla to Volkswagen actively setting up their own battery plants. This trend of vertical integration is changing traditional supplier relationships.
The raw material supply landscape is also undergoing profound changes. The demand for key minerals such as lithium, nickel, and cobalt has surged, leading to significant price volatility. For example, the price of lithium soared to $60,000 per ton in 2022, nearly 10 times higher than at the end of 2020. This volatility has placed immense pressure on the entire supply chain. Automakers and battery manufacturers are moving upstream in the supply chain, directly investing in mines to secure raw material supplies.
The production and manufacturing processes are also facing significant adjustments. NEVs have a higher degree of modularization, requiring greater flexibility in production lines. For instance, a single production line may need to accommodate models with different battery capacities simultaneously. This demands that the supply chain has the ability to respond quickly and support flexible production.
Additionally, the after-sales service system for NEVs is being restructured. The traditional 4S dealership model is being replaced by a new model of online direct sales combined with offline service centers. This change requires the supply chain to support more precise and timely parts supply and technical support.
Suppliers within the automotive supply chain are also facing significant challenges in their transformation and upgrading. An executive at a medium-sized supplier of traditional internal combustion engine components admitted, "We are facing an unprecedented survival crisis. The demand for our existing products in the NEV sector is rapidly declining, but transitioning to electrification requires massive investment and entirely new technological capabilities." This dilemma is not unique. According to a McKinsey survey, more than 60% of traditional auto parts suppliers believe they lack the necessary resources and capabilities to cope with the transition to electrification. In response to this challenge, some suppliers are choosing strategic transformation, such as shifting from producing transmissions to manufacturing electric drive systems. Others are rapidly acquiring new energy technology and market access through mergers or joint ventures.
A seasoned automotive industry consultant noted, "The automotive supply chain in the new energy era requires agility and innovation more than ever. Only those companies that can quickly adapt to changes and proactively innovate will stand out in this transformation."
Indeed, in the face of such drastic changes, the entire automotive industry chain needs to rethink its positioning and value proposition. Traditional suppliers need to transform quickly and seek new growth points. Emerging players need to rapidly build scale and quality advantages. Automakers must innovate while constructing stable and efficient supply networks.
This transformation brings not only challenges but also opportunities. Companies that can proactively plan, adapt flexibly to changes, and seize the opportunities of the new energy era are likely to lead the industry’s future. However, to achieve this goal, companies must overcome numerous challenges. Next, we will delve into the main challenges facing the new energy supply chain and potential strategies to address them.
As one industry expert put it, "We are living in an exciting era. The new energy revolution is not just a product innovation but a reconstruction of the entire industry ecosystem. In this process, the importance of the supply chain has become more prominent than ever. Those who can build a more intelligent, resilient, and sustainable supply chain will gain a competitive edge in the future."
Battery Supply Chain: The Lifeblood and Challenges of New Energy Vehicles
In the supply chain of new energy vehicles (NEVs), the battery undoubtedly stands as the most crucial element. It not only determines the vehicle's performance and cost but also profoundly influences the trajectory of the entire industry. However, the battery supply chain faces unprecedented challenges that require collective efforts across the industry to overcome.
The first and foremost challenge is the uncertainty in the supply of raw materials. Imbalances in the supply and demand of key minerals like lithium, nickel, and cobalt have led to dramatic price fluctuations, directly impacting battery costs. An industry analyst pointed out, "In 2022, the price of battery-grade lithium carbonate surged nearly tenfold from the end of 2020, putting enormous pressure on the entire supply chain." To address this challenge, more and more automakers and battery manufacturers are extending their reach upstream. For instance, BYD acquired lithium mines in Chile, while Tesla signed long-term supply agreements with Australian mining companies. "While vertical supply chain integration can mitigate raw material risks to some extent, it also increases capital expenditure and management complexity for companies," noted a supply chain expert.
The uncertainty in technological pathways also poses a challenge to the battery supply chain. From lithium iron phosphate to ternary lithium batteries, and from solid-state batteries to sodium-ion batteries, competition among different technologies continues. This uncertainty not only affects companies' investment decisions but also adds complexity to the supply chain. "We must maintain enough flexibility to adapt to possible technological changes," said the CTO of a leading battery manufacturer. "This means we need to build a more agile and modular supply chain."
Balancing large-scale production with quality control is another major challenge. As demand for electric vehicles (EVs) grows rapidly, battery manufacturers face pressure to quickly expand their capacity. However, battery quality is directly related to vehicle safety and leaves no room for compromise. A quality control expert emphasized, "While pursuing speed, we must not overlook quality. This requires us to continuously optimize production processes and strengthen quality management throughout the entire process."
In response to these challenges, the industry is actively exploring innovative solutions. Among them, the application of the circular economy concept is particularly noteworthy. Battery recycling and secondary use are becoming important ways to alleviate raw material pressure and reduce environmental impact. It is estimated that by 2025, over 1 million tons of retired power batteries will need to be processed globally. This presents both a challenge and an opportunity.
"We are establishing a closed-loop supply chain," said the CEO of a leading battery recycling company. "Retired batteries are no longer waste but valuable sources of raw materials." With advanced recycling technologies, they can recover over 95% of key metals, which not only reduces raw material costs but also significantly decreases environmental impact.
Secondary use is another important direction. Although retired batteries may no longer be suitable for automotive use, they can still be utilized in energy storage and other fields. For example, CATL has partnered with the State Grid Corporation of China to use retired power batteries for grid peak-shaving. "This greatly extends the life cycle of batteries and improves resource utilization efficiency," explained an engineer involved in the project.
Standardization and modular design are also key strategies for addressing supply chain challenges. For example, Volkswagen's MEB platform is a great example. By standardizing the size and interface of battery packs, not only does it simplify supply chain management, but it also enhances production flexibility. "This allows us to respond more quickly to changes in market demand, while also leaving room for future technology upgrades," said a Volkswagen executive.
The application of digital technologies is also transforming the battery supply chain. From blockchain-enabled raw material traceability to AI-optimized battery management systems, and IoT-supported full life cycle monitoring, digitalization is injecting new vitality into the battery supply chain. "Digital twin technology allows us to simulate and optimize the entire supply chain in a virtual environment," explained a technology expert. "This greatly enhances our decision-making efficiency and accuracy."
Looking ahead, the development of the battery supply chain will continue to face challenges, but the opportunities are equally vast. Companies that can effectively integrate resources, drive technological innovation, and practice circular economy principles will gain an edge in this transformation. As one industry leader put it, "Batteries are not only the heart of NEVs but also the core of the entire clean energy revolution. Those who can achieve breakthroughs in the battery supply chain will lead the future of the entire industry."
Undoubtedly, the optimization and innovation of the battery supply chain will remain the focus of the NEV industry. It is not only about the success or failure of individual companies but will also deeply impact the sustainable development of society as a whole. In this challenging and opportunity-filled field, innovation, collaboration, and long-term vision will be the keys to success.
Digital Technology Empowering the New Energy Vehicle Supply Chain
As the new energy vehicle (NEV) industry rapidly evolves, digital technology is profoundly transforming the entire supply chain. From raw material procurement to final product delivery, and from demand forecasting to inventory management, digitalization is bringing unprecedented opportunities to this challenging industry.
Some issues are unique to the NEV sector. For example, the coordination between charging infrastructure construction and supply chain management is a particularly tricky problem. By the end of 2022, the number of NEVs in China had exceeded 13 million, while the number of public charging stations stood at only 1.7 million. The difficulty in charging has severely constrained the widespread adoption of NEVs. This not only affects sales but also introduces uncertainty into supply chain planning. As one industry expert noted, "The lag in charging infrastructure compared to vehicle growth may lead to a sudden market demand drop, thereby impacting the entire supply chain." In response, some forward-looking car companies have begun to include charging infrastructure in their overall supply chain planning. For instance, Tesla's Supercharger network not only serves users but also plays a crucial role in its supply chain by optimizing delivery routes and reducing logistics costs. Addressing these issues requires the latest digital technologies to empower supply chain management.
Artificial intelligence (AI) and machine learning are particularly prominent in demand forecasting and inventory management. The NEV market is fast-changing and highly uncertain, rendering traditional forecasting methods inadequate. As one supply chain expert pointed out, "In the electric vehicle sector, we are dealing with an entirely new market where historical data has limited reference value." AI algorithms can integrate multidimensional data, including policy changes, charging infrastructure distribution, and consumer preferences, to make more accurate predictions. For example, a leading electric vehicle manufacturer uses AI to analyze charging data, vehicle usage patterns, and social media sentiment to accurately forecast the demand for different battery models, significantly improving supply chain responsiveness.
The Internet of Things (IoT) technology is comprehensively enhancing supply chain visibility, which is particularly crucial in battery supply chain management. "The battery is the heart of an NEV, and its performance and safety are paramount. IoT allows us to monitor the battery's status throughout its lifecycle," said an executive from a battery manufacturer. By installing smart sensors on batteries, companies can monitor key indicators such as temperature, charge cycles, and remaining capacity in real-time. This not only aids in quality control but also provides valuable data for product optimization and after-sales service. More importantly, this end-to-end visibility greatly enhances supply chain resilience, enabling companies to quickly identify and resolve potential issues.
Automation and robotics are reshaping the production and logistics processes in the NEV industry. Compared to traditional vehicles, electric vehicles have a simpler structure, making them more suitable for automated production. A leading electric vehicle manufacturer has introduced hundreds of robots in its gigafactory, achieving a high level of automation from battery assembly to final vehicle production. This not only greatly improves production efficiency but also ensures product consistency and reliability. In warehousing, Automated Guided Vehicles (AGVs) are widely used. A logistics manager explained, "AGVs can precisely locate and transport battery packs weighing several tons and can communicate in real-time with the warehouse management system to optimize inventory layout."
Blockchain technology offers new possibilities for addressing raw material traceability and supply chain transparency in the NEV industry. The supply of key minerals such as lithium and cobalt often involves complex international trade and ethical issues. Several car companies are experimenting with blockchain technology to track the sources of these raw materials. "Blockchain allows us to ensure that every raw material used in our batteries comes from legitimate and sustainable sources," said an engineer involved in the project. This not only aids in supply chain management but also enhances brand reputation.
However, digital transformation also presents several challenges. The first is the significant upfront investment required. As one CIO acknowledged, "Digital transformation is not just a simple technology upgrade but a complete overhaul of the business model. This requires substantial capital and long-term commitment." Secondly, there is a talent shortage. The NEV industry already faces a shortage of talent, and digital transformation exacerbates this issue. A human resources manager noted, "We need professionals who understand both the automotive industry and digital technology, but such talent is extremely scarce in the market."
Moreover, data security and system integration are challenges that companies must confront. As the supply chain becomes increasingly digitalized and interconnected, cybersecurity risks rise. This issue is particularly sensitive in the NEV industry, which involves core technologies and customer data.
Despite these challenges, the trend toward digital transformation is irreversible. Companies that effectively leverage digital technology will gain a competitive edge in the future. As one industry observer stated, "In the new energy era, the most competitive supply chains will be digitalized, intelligent, and highly integrated ecosystems. They will not only be efficient but also able to quickly adapt to market changes and continually innovate."
Sustainable Development: The Inevitable Path for New Energy Vehicle Supply Chains
Amid the wave of the new energy vehicle (NEV) revolution, sustainability has become a core issue for the entire industry. This shift is driven not only by environmental policies but also by market and consumer demand. As one industry leader put it, "Producing 'green' cars while neglecting supply chain sustainability is like treating the symptoms but not the cause. True sustainability must permeate the entire value chain."
The goal of achieving carbon neutrality is pushing the green transformation of supply chains. Major automakers have announced ambitious carbon reduction plans. For example, the Volkswagen Group has committed to achieving carbon neutrality across its entire value chain by 2050. To meet this target, companies are re-evaluating every aspect of their supply chains. A supply chain manager described their transformation journey: "We are now looking at supplier selection with a new perspective. Carbon footprint has become as critical as cost and quality in our supplier evaluations."
This shift is reshaping the entire supply chain landscape. Energy-intensive component production is increasingly moving to regions rich in renewable energy. For instance, CATL has established the world’s largest power battery production base in Qinghai, leveraging the abundant local solar and wind energy resources. A company executive explained, "Here, we can produce batteries using 100% clean energy, significantly reducing the carbon footprint of our products."
The practice of circular economy principles within the NEV supply chain is also becoming more widespread. Battery recycling and second-life utilization have emerged as key areas of focus. By 2025, it is estimated that over 1 million tons of retired power batteries will need to be processed globally. This presents both challenges and opportunities. The CEO of a leading battery recycling company remarked, "We are building a closed-loop supply chain. Retired batteries are no longer waste but valuable sources of raw materials." Through advanced recycling technologies, they can recover over 95% of critical metals, reducing material costs and minimizing environmental impact.
Forward-thinking automakers are integrating sustainability into product design from the outset. For example, BMW's i3 electric vehicle extensively uses recyclable materials, with 95% of the vehicle's components being recyclable after its lifecycle ends. "Sustainability shouldn't be an afterthought but a core element considered from the conception stage of the product," a BMW designer commented.
However, driving sustainability in supply chains is not without its challenges. The first is the cost. Green technologies and materials often require higher initial investments. A CFO admitted, "In the short term, this will impact our profit margins. But in the long run, it's a necessary investment to remain competitive." Then, there are the technological challenges. Battery recycling technologies are still evolving, and the economic feasibility of large-scale recycling has yet to be fully proven. Additionally, the complexity of global supply chains presents obstacles to sustainable development. As an expert pointed out, "Ensuring that every link in a globalized supply chain meets sustainability standards is a daunting task. This requires unprecedented transparency and collaboration."
In response to these challenges, more companies are adopting innovative approaches. For instance, Tesla is exploring a model that combines carbon credit trading with supplier management. Suppliers can earn carbon credits by improving energy efficiency, using renewable energy, or other means. These credits can offset their carbon emissions or be sold to other companies. "This creates a win-win situation," explained a senior executive involved in the project. "Suppliers are incentivized to become greener, we gain a more sustainable supply chain, and the entire ecosystem benefits."
Policy support also plays a crucial role. China's power battery traceability policy is a prime example. This policy mandates that all power batteries for NEVs must have unique identification information, enabling full lifecycle traceability. "This not only facilitates battery recycling and reuse but also raises the standards for the entire industry," a policy researcher commented.
Looking ahead, sustainability will continue to reshape the NEV supply chain. Companies that can deeply integrate sustainable practices into their business models will gain a competitive edge in the future. As one industry leader stated, "In the new energy era, the most successful companies will not just be those that sell cars but those that provide sustainable mobility solutions. This requires a completely different mindset and business model."
Future Outlook: Building Intelligent, Resilient, and Sustainable Supply Chains for New Energy Vehicles
Following the dual transformation of digitalization and sustainability, the supply chain for new energy vehicles (NEVs) is evolving towards greater intelligence, resilience, and sustainability. This evolution is not only the result of technological advancements but also a fundamental shift in the industry's mindset. As an industry leader puts it, "We are no longer just manufacturing cars; we are reshaping the entire mobility ecosystem." Deep industry collaboration is becoming the new norm in the NEV sector. Traditional supplier relationships are no longer sufficient to meet the rapidly changing market demands. Increasingly, car manufacturers are forming deeper partnerships with suppliers, technology companies, and even competitors. For example, Volkswagen's collaboration with Ford on electric vehicle platforms and Toyota's alliance with Panasonic on battery technology reflect this trend. A strategic expert explains, "In the era of new energy, no company can tackle all challenges alone. Building a strong ecosystem is more advantageous than going solo."
This collaboration extends beyond technology to all aspects of the supply chain. For instance, several car manufacturers are partnering with mining companies to jointly develop and manage the supply of critical raw materials. Tesla has even invested directly in lithium mines to ensure a stable supply of battery materials. "This vertical integration strategy allows us to better control costs and quality while also enhancing the resilience of the supply chain," says a Tesla executive.
The balance between localized production and global procurement is being redefined. The COVID-19 pandemic and geopolitical factors have exposed the vulnerabilities of global supply chains, driving the trend towards localized production. However, global procurement remains crucial for cost reduction and access to advanced technologies. A supply chain expert notes, "The key is to establish a flexible and diversified supply network. We need to find a balance between efficiency and resilience."
We see more car manufacturers adopting a "partial globalization" strategy. For example, Hyundai's electric vehicle factory in Georgia, USA, not only serves the North American market but also becomes a key node in its global supply chain. "This not only reduces logistics costs and tariff risks but also allows us to respond more quickly to local market demands," explains a Hyundai executive.
Talent development and skill upgrading are key challenges for building future supply chains. The NEV supply chain requires not only traditional automotive engineers but also data scientists, software engineers, sustainability experts, and other multi-disciplinary talents. A human resources executive admits, "We face not only a shortage of talent but also a fundamental shift in skill requirements."
Policy support and the improvement of industry standards will also play a crucial role in shaping the future supply chain. Governments worldwide are promoting the development of the NEV industry through various policy measures. For example, China's dual-credit policy and the European Union's carbon emission regulations are profoundly affecting the layout and operation of the entire supply chain. A policy researcher points out, "In the future, carbon pricing mechanisms are likely to become a global standard. This will completely alter the cost structure of the supply chain and drive the industry towards a low-carbon transition."
At the same time, the formulation of industry standards is accelerating. From battery specifications to charging interfaces, and from raw material traceability to recycling, a series of standards are being established. This will not only benefit from economies of scale but also promote the healthy development of the entire ecosystem.
Looking ahead, the NEV supply chain will continue to evolve towards greater intelligence, resilience, and sustainability. Digital technologies will permeate the entire value chain, enabling end-to-end visibility and intelligent decision-making. Sustainability will no longer be an add-on but a core competency. The boundaries of the supply chain will become increasingly blurred, and cross-industry, cross-sector collaboration will become the norm.
"Future competition will no longer be between individual companies but between entire ecosystems. The company that builds the strongest and most flexible ecosystem will stand out in this new energy revolution."
===========
The content of this article is reproduced from: WeChat Official Account - DSC Digital Supply Chain. The article only represents the author's views. If you have any suggestions or questions, please contact me.
DSC (Digital Supply Chain) is positioned to bring together the country's top digitalization & supply chain experts to jointly discuss professional issues and cutting-edge hotspots in the field of large supply chains, and explore the development direction of supply chains in the field of digitalization.
END

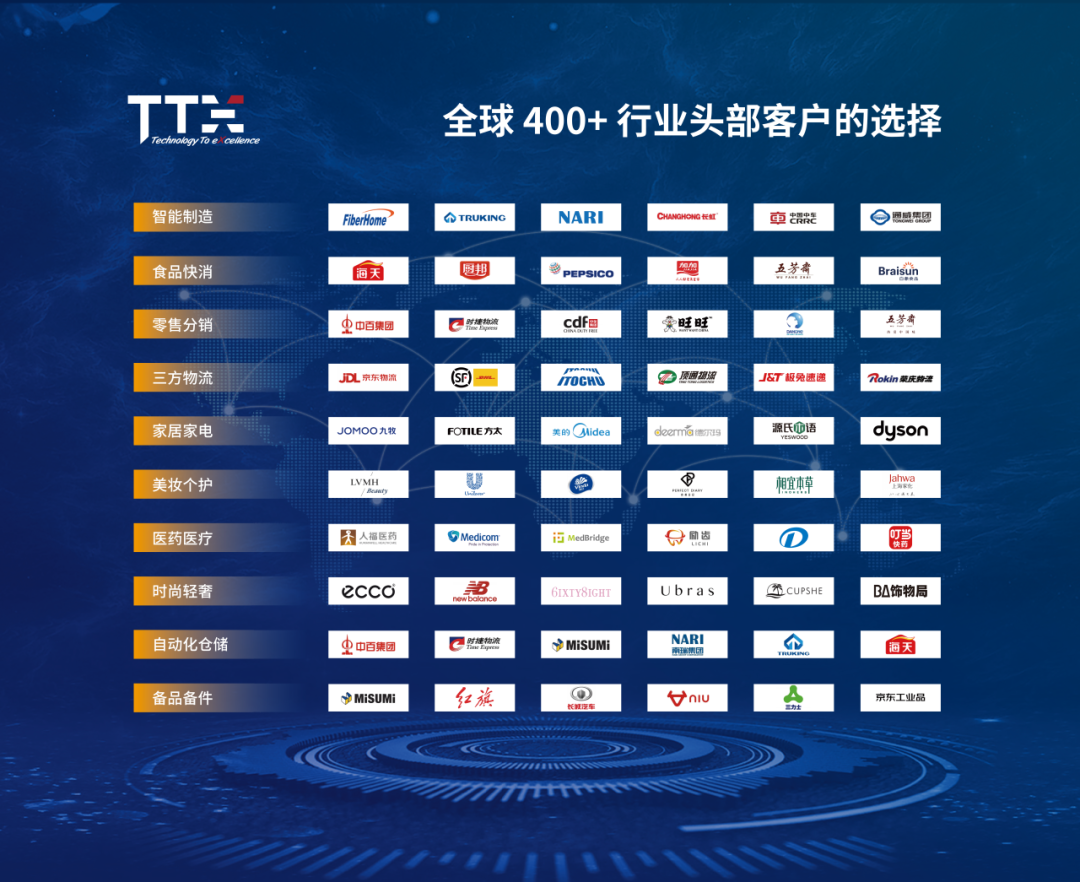
Share