The Integration of IT and OT: Core Concept of Smart Manufacturing
-
2024-09-14
Introduction: In today’s rapidly changing business environment, the manufacturing industry is facing unprecedented challenges and opportunities. Digital transformation is no longer a choice but a necessity for survival. In this transformation, the integration of Information Technology (IT) and Operational Technology (OT) is becoming a key driving force behind smart manufacturing. This article will delve into how this integration is reshaping the future of manufacturing and how companies can address the challenges brought by this transformation.
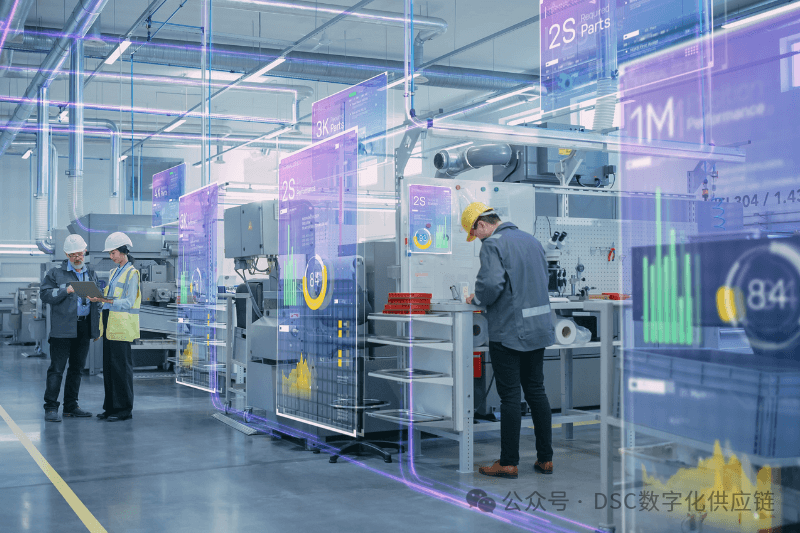
Imagine a modern smart factory where every piece of equipment on the production line is in real-time communication with the central control system. When a machine detects a slight performance deviation, it not only adjusts its parameters immediately but also communicates this information across the entire production network. Meanwhile, the supply chain management system is adjusting raw material orders and production schedules based on this real-time data. This is the transformation brought about by the integration of Information Technology (IT) and Operational Technology (OT).
Traditionally, IT and OT have been two parallel worlds. IT primarily manages enterprise information systems such as ERP and CRM, focusing on data processing and business process management. OT, on the other hand, is responsible for monitoring and controlling physical equipment and processes, ensuring production stability and efficiency. These two domains have long operated in isolation, leading to the creation of information silos, which have hindered the comprehensive digital transformation of businesses.
However, with the advent of Industry 4.0, the integration of IT and OT has become inevitable. As Flexware’s Chief Architect Brent Maringer pointed out, "New platform technologies are forcing us to rethink who owns what, and why they own it." This integration is not just a merging of technologies but a shift in mindset. The fusion of IT and OT presents manufacturing enterprises with unprecedented opportunities.
Firstly, it enables end-to-end visibility and control. From raw material procurement to the delivery of finished goods, every step can be monitored and optimized in real-time. This holistic view allows businesses to respond more quickly to market changes and increases production flexibility. Secondly, the integration promotes the development of predictive maintenance. By combining IT's data analytics capabilities with OT’s real-time monitoring data, companies can accurately predict equipment failures, significantly reducing unplanned downtime and improving equipment utilization. As ACE expert Craig Egan emphasized, "Facts are more important than data." Here, "facts" refer to valuable information derived from analysis and context, rather than raw data.
Lastly, the integration of IT and OT opens new doors for innovation. For example, the application of digital twin technology allows companies to simulate and optimize production processes in a virtual environment, greatly shortening product development cycles and reducing trial-and-error costs. However, this integration is not without its challenges. "The evolutionary paths of IT and OT technologies are different." These differences are not only technological but also cultural and ideological. IT departments are accustomed to rapid iteration and frequent updates, whereas OT departments prioritize stability and reliability. Balancing innovation while ensuring production stability has become a crucial challenge for businesses.
Technical Perspective: Breaking Data Silos and Building a Unified Information Model
Organizational Transformation: Cross-Department Collaboration and Talent Development
In the process of IT and OT integration, while technology plays a crucial role, the real challenge often lies in people and organizational structures. As Craig Egan emphasized, "It’s not just a technology issue, it’s a cultural issue." To successfully integrate IT and OT, businesses must break down traditional departmental silos, cultivate new types of talent, and reshape organizational culture.
One of the most critical steps is eliminating the silos between IT and operations departments. Historically, these two departments have often operated independently, sometimes with conflicting attitudes. The IT department may feel that the operations team doesn’t appreciate the importance of modern technologies, while the operations team might think IT solutions are disconnected from reality. As Brent Maringer described, "There has often been an 'us versus them' mentality." Changing this dynamic requires leadership commitment and specific actions. Some successful companies have adopted the following strategies:
- Cross-Departmental Task Forces: These groups consist of members from both IT and operations, tasked with driving specific integration projects. Working together helps each side understand the other's needs and challenges better.
- Job Rotation Programs: IT staff spend time working on the factory floor, while operations staff participate in IT projects. This firsthand experience significantly enhances mutual understanding.
- Shared KPIs: Setting cross-departmental key performance indicators (KPIs) encourages IT and operations to work toward common goals.
- Top-Level Support: Leadership must explicitly endorse integration and reflect this in resource allocation and decision-making processes.
Cultivating talent with interdisciplinary skills has become a key priority. As Jonathan Wise pointed out, "IT professionals need to understand OT, and OT professionals need to acquire IT skills." This cross-disciplinary knowledge not only facilitates technical integration but also promotes better communication and collaboration between teams.
Some forward-thinking companies have already taken action. For example, a large manufacturer has introduced a new role called "Digital Engineer." These engineers are well-versed in traditional manufacturing processes as well as data analytics and software development, acting as bridges between the IT and OT worlds. Another company partnered with local universities to establish specialized courses on smart manufacturing, preparing future talent with cross-disciplinary expertise.
In the process of reshaping organizational culture, leaders need to lead by example and demonstrate the value of cross-departmental collaboration. For instance, former GE CEO Jeff Immelt personally participated in digital transformation projects, sending a strong message about the urgency of change. This kind of top-down transformation often has a lasting impact on the organization.
However, cultural change does not happen overnight. As one manufacturing executive put it, "Changing technology may take months, but changing mindsets can take years." Therefore, companies need to be patient, invest resources consistently, and reinforce new cultural ideas through various means.
For example, Siemens introduced a "Digital Ambassadors" program in its digital factories. These ambassadors, employees from different departments, receive specialized training and are responsible for promoting digital practices in their daily work. Through this approach, Siemens successfully permeated the digital culture throughout the organization.
Another emerging trend is the rise of "citizen developers." With the increasing popularity of low-code and no-code platforms, more non-IT personnel are getting involved in software development. This not only alleviates pressure on IT resources but also fosters deeper integration between business and technology. However, management faces new challenges in balancing innovation with system stability.
In addition to technical skills, soft skills are becoming increasingly important in the context of IT-OT integration. Communication, problem-solving, and teamwork are critical for success in this environment. Some leading companies have already started incorporating these soft skills into their employee training and evaluation systems.
Finally, change management plays a vital role in IT-OT integration. This integration often leads to significant adjustments in workflows and responsibilities, which can cause anxiety and resistance among employees. Effective change management strategies, including clear communication, comprehensive training, and appropriate incentive mechanisms, are key to ensuring a smooth transition. As Craig Egan emphasized, "This is a journey, not a sprint." Businesses must adopt a long-term perspective and consistently invest in order to truly achieve deep IT-OT integration and unlock the full potential of smart manufacturing.
In conclusion, successful IT-OT integration requires more than just technological advancements. It demands a comprehensive organizational transformation, driven by collaboration, talent development, and cultural change. Those companies that can effectively manage these aspects will be better positioned to lead in the era of smart manufacturing.
Implementation Path: Step-by-Step Approach with a Focus on Practical Results
===========
The content of this article is reproduced from: WeChat Official Account - DSC Digital Supply Chain. The article only represents the author's views. If you have any suggestions or questions, please contact me.
DSC (Digital Supply Chain) is positioned to bring together the country's top digitalization & supply chain experts to jointly discuss professional issues and cutting-edge hotspots in the field of large supply chains, and explore the development direction of supply chains in the field of digitalization.
END

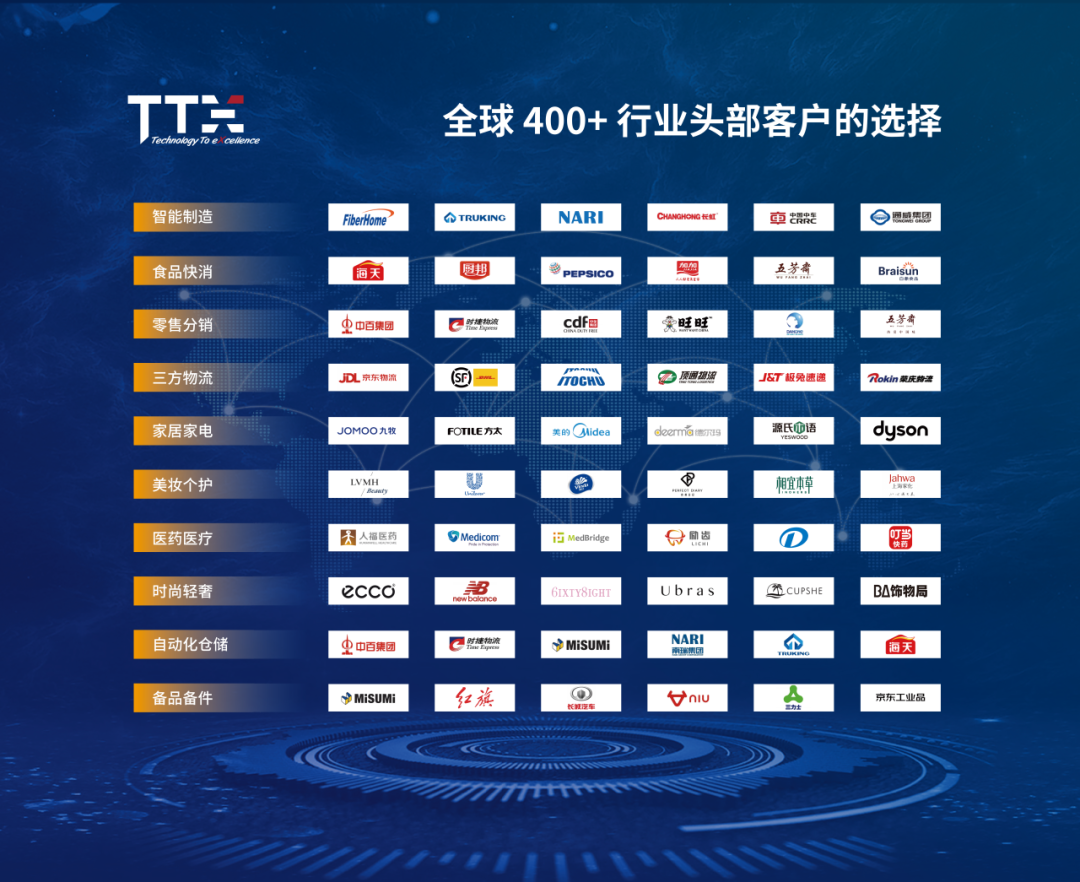
Share