-
Intelligent Manufacturing
-
Automated Warehousing
-
Warehouse Management System
How does China's leading pharmaceutical equipment company, Truking, manage 600,000 materials and over 30 warehouses?
By analyzing Truking's information management, operational management, and warehousing operations, TTX provided a digital in-plant logistics solution. This solution encompasses everything from inbound to outbound logistics, inventory searching for outbound orders, delivery acceptance, comprehensive inventory management, task scheduling, and equipment coordination. This is one of the most comprehensive cases in the manufacturing industry. It not only meets the operational requirements of over 30 warehouses and multiple owners but also fulfills the need for precise management of over 600,000 materials.
-
30+
warehouses with multiple owners
-
600,000+
materials precisely managed
-
2x
improvement in labor efficiency
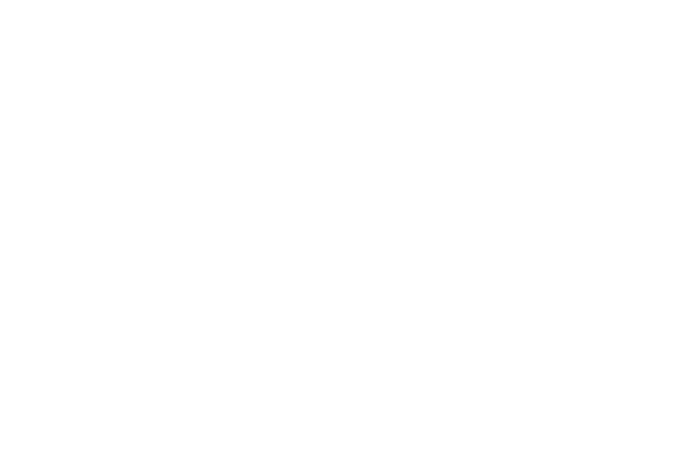
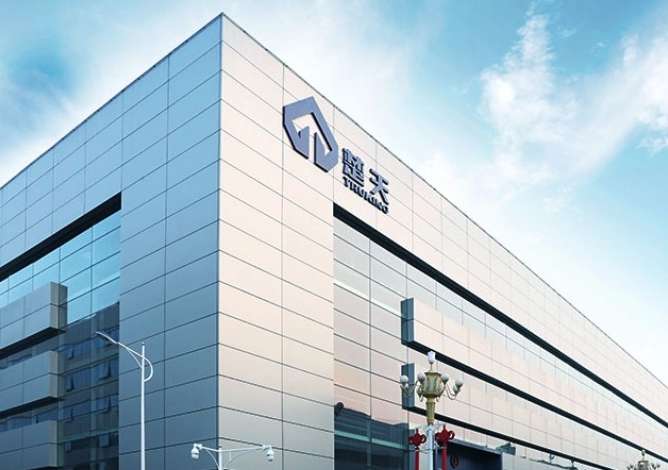
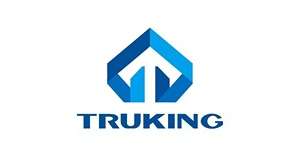
The manufacturing industry is the foundation and cornerstone of a country's strength. Over the past decade, China's manufacturing industry has achieved remarkable development, continuously moving from the middle and low-end to the middle and high-end sectors. In the pharmaceutical equipment industry, which integrates pharmaceutical processes, chemical machinery, automatic control, and other specialties, there has been significant progress. In recent years, with the gradual filling of domestic gaps and performance verification in the field of COVID-19 vaccines, high-end pharmaceutical equipment has gradually achieved domestic substitution, breaking the previous foreign monopoly in this sector.
After years of hard work, Truking, a leading domestic medical equipment enterprise, now stands shoulder to shoulder with imported equipment. During the COVID-19 pandemic, Truking undertook the supply of nearly 80% of the core equipment and process technologies for the production of Chinese COVID-19 vaccines, making significant contributions to China's fight against the pandemic.
Truking is known to own or control several wholly-owned or holding subsidiaries, including Germany's ROMACO Group, Chutian Huatong, Sichuan Pharmaceutical Design Institute, Chutian Feiyun, Chutian Yuanchuang, and Chutian Intelligent Robotics, among others. With total assets approaching tens of billions of yuan, its products cover a wide range of categories including liquid drug equipment, solid preparation equipment, and powder drug equipment.
Both the rapid growth of its business and the trend towards high-precision development in pharmaceutical equipment demand higher standards for operational stability, reliability, and automation. This necessitates a more agile and precise response capability throughout its manufacturing supply chain.
To meet these requirements, Truking has introduced new intelligent logistics equipment for efficient production. On the software front, Truking possesses the capability to develop and build intelligent warehousing and logistics systems, primarily serving downstream pharmaceutical enterprises. While it previously utilized ERP and MES systems for upstream operations, with ERP managing warehousing operations, these existing systems were evidently inadequate to support its evolving needs.
In the face of the new competitive environment in the era of Industry 4.0, Chutian has set high requirements for its self-owned warehouse management system. The key challenge for Chutian is how to use a comprehensive digital supply chain system to shorten response times between various links in the supply chain, manage the entire supply chain including internal supply chain management, production planning coordination, and logistics management, reduce human dependency, achieve standardized management, and efficient operations.
In 2021, Truking, along with its subsidiaries Chutian Feiyun and Chutian Yuanchuang, approached TTX with a request to introduce a digital supply chain system to transform factory logistics.
Digitalized Factory Logistics Solution
After analyzing Truking's information management, operational management, and warehouse operations, TTX provided a comprehensive digitalized factory logistics solution. This solution integrates functions from inbound to outbound processes, order picking and inventory locating, distribution verification, global inventory management, task scheduling, and collaborative equipment handling. It stands as a comprehensive example in the manufacturing industry, meeting operational requirements across more than 30 warehouses with multiple owners, and addressing the precise management needs of over 600,000 materials.
Comprehensive Function Integration in Manufacturing
Previously, under the existing operational and information management models, there was insufficient integration and process control between upstream and downstream operations at the factory and warehouse levels. Information synchronization between these stages was lacking automated capabilities. TTX's WMS system addressed this by integrating with Chutian's upstream SAP, MES, OA, QMS, and other systems, enhancing data circulation efficiency and accuracy between departments. This ensures that all data passing through the WMS system complies with Chutian's plans and requirements.
For instance, adjustments to documents before inbound processes and real-time retrieval of the latest upstream documents during warehouse receipt processing are critical. TTX's WMS system integrates with SAP and MES systems to ensure that every detail of inbound receipts aligns with Chutian's plans. Integration with the OA system ensures the accuracy of system workflows, with all data sent to the WMS being confirmed through specified approval processes. Integration with QMS ensures inbound material quality meets requirements.
In this project, apart from upstream systems, TTX's WMS also integrates with 32 physical and virtual warehouses under Truking, Chutian Feiyun, and Chutian Yuanchuang, including 2 automated warehouses such as AGV-based automatic warehouses and high-rack stereo material box libraries. Integration with downstream warehouses not only enhances warehouse automation and efficiency but also distinguishes between attributes of stand-alone and flat storage, facilitating orderly material handling.
Through integration with multiple upstream and downstream systems, the Chutian project exemplifies comprehensive function integration in the manufacturing industry, effectively connecting various systems and managing inventory across subsidiary companies.
Unified Management of Over 30 Warehouses
You might wonder how a manufacturing enterprise with over 30 warehouses and 3 owners manages to unify its operations.
The warehouse operations in manufacturing are complex and diverse. Just the inbound processes alone involve multiple business scenarios: raw material receipts, finished product receipts, each requiring flexible system operations. Different inbound processes are configured based on business scenarios to automatically distinguish operations and prevent human errors, which becomes even more critical when dealing with over 30 warehouses.
According to reports, TTX surveyed representative warehouses such as central warehouses and rear packing warehouses, and re-planned unified operational and management processes according to Chutian's requirements.
Truking has multiple production factories within and outside its industrial park, each equipped with a warehouse that doesn't serve the factory exclusively and may also hold inventory for other factories. During production, manufacturing departments proactively requisition materials from the warehouse department. In such cases, some common materials might accumulate in certain factories, leading to incidents like production line shortages due to multiple factories competing for materials.
Truking's largest warehouse, the central warehouse, also faces such challenges. To minimize inter-department disputes, TTX addressed issues related to independently managing goods from multiple owners spread across multiple warehouses, solving problems such as locating inventory and splitting orders during outbound operations. Additionally, TTX assisted Chutian in transitioning from a requisition-based to a distribution-based model by establishing a designated distribution area between warehouses and factories. When urgently needed, factories scan and claim materials, establishing a controlled delivery handover system between factory departments and warehouse departments.
In this process, TTX's WMS ensures accuracy in inter-departmental handovers through its verification function. It enhances the efficiency of document processing through real-time interfaces with upstream systems and automation, and improves traceability of documents and goods through multidimensional reports and system records of goods and document flows.
In the rear packing warehouse, TTX's WMS integrates AGVs and automated high-rack warehouses, establishing standard processes for automated operations such as inbound, shelving, inventory checking, inventory allocation, and outbound operations tailored to different material management needs.
Through such redesigned processes extended to warehouses with similar characteristics, the project achieved rapid deployment within six months. Notably, TTX's WMS enhances configurability to a new level, allowing rapid deployment of new warehouses through system rules adjustments by Chutian's internal personnel, without altering the source code, thereby reducing operational difficulties and long-term maintenance costs.
Precision Management of Over 600,000 Items
Pharmaceutical equipment belongs to the category of non-standard products, often requiring special customization according to customer needs, with different products and dosage forms requiring corresponding equipment and production lines. According to reports, Chutian manages over 600,000 items, necessitating high precision in inventory management. Due to high turnover rates, there is rarely any stockpile or redundancy in inventory, necessitating warehouses to respond in real-time to factory production demands.
In response to Chutian's requirements for precision management, TTX has implemented comprehensive measures to establish standardized and normalized warehouse business processes.
In the past, management of internal logistics heavily relied on human experience, with interactions between various operational stages carried out through primitive paper-based processes or supplementary recording systems. Operations mostly relied on manual intervention, resulting in heavy workloads, high error rates, and discrepancies between inventory and actual goods due to non-standard business operations.
Recognizing this, TTX replaced manual experience with its WMS system, seamlessly supporting operations on both PC and RF terminals. For instance, in outbound operations: PC users only need to select batches and execute the corresponding tasks with a single click, while RF terminals confirm the quantity and product information for outbound tasks. In daily operations, the WMS system synchronously prompts tasks, allowing warehouse operators to view tasks on PDAs, reducing paper documents. Moreover, by adopting PDA scanning throughout the operation process, data collection and verification shifted from manual to automatic, significantly enhancing operational efficiency and accuracy.
Another crucial reform involved barcode and warehouse zone management. Previously, Chutian YuanChuang's warehouse management lacked structured zone and location management, with most goods lacking barcode management. TTX's WMS integrated electronic labeling devices for standardized goods labeling, establishing unified material files and barcode labeling standards. It also implemented unified coding and zoning plans for facilities such as warehouses, zones, and locations. Operators can now perform precise inbound and outbound operations by scanning product labels, minimizing human errors caused by manual operations and enhancing the accuracy of FIFO (first-in, first-out) for finished products and raw materials.
Furthermore, TTX's WMS enabled the customization of six product attributes, managed by factors such as factory, batch, and project. It also facilitated batch conversion or fixed material properties based on order conditions through transfer documents, ensuring traceability of overall inventory.
Additionally, TTX developed a planning system solution: MES provided production and material plans after decomposition, with rolling releases for monthly, weekly, and daily plans (e.g., locking in daily requirements two days in advance). Warehouse planners promptly queried material requirements based on production plans, and WMS generated picking batches according to demand rhythms, creating distribution plans. Distribution planners promptly arranged vehicle and driver schedules for pickup and delivery based on distribution plans. Multiple personnel could timely access, modify, and track plan completions.
Through these measures, Chutian not only enhanced the precision of warehouse goods management but also achieved coordination across sales plans, production plans, procurement plans, material requirement plans, inbound plans, picking plans, and distribution plans.
Conclusion
"In the feedback from Chutian, except under special circumstances, warehouse operators no longer need to work overtime for shipping and receiving. At the same time, warehouse accuracy management has also improved significantly, with system data closely matching physical inventory, effectively resolving issues that previously impacted production due to warehouse stock problems," said Tang Jieyang, project manager of Tongtianxiao.
It is reported that, under equivalent conditions of inbound and outbound volumes, Chutian's warehouse efficiency has more than doubled on average, with reduced potential for operational errors through system management. Additionally, various types and dimensions of reports such as outbound, inbound, and transfers can be updated in real-time and exported at any time. This capability supports process flow management across production line requisitions, production, completion, semi-finished goods management, and finished goods management, achieving visualization of the entire supply chain business process and providing a basis for management decisions.
Further elaborating on this, Tang Jieyang stated, "When issues arise in the system, employees can pinpoint the exact nature of the problem, whether it's related to interfaces, APIs, or document repositories. They can also clearly understand daily shipment volumes, expected shipment volumes, or expected receipt volumes versus actual receipt volumes. Through these insights, the system establishes a reporting mechanism and system error handling."
Overall, since the project went live, it has not only enhanced operational efficiency and accuracy in warehouse operations but also made the warehouse fully visible and traceable.
Amidst the trends of digitalization, lean operations, and intelligent manufacturing in the manufacturing industry, a glance at Chinese factories reveals that many still operate in primitive manual logistics modes. Software remains largely separated from hardware, with standalone ERP, OA systems, making it difficult to achieve true "software-hardware integration." Moreover, the idea of mapping the digital world into the physical world to break real-world constraints and achieve flexible manufacturing seems distant. According to research observations by certain agencies on frontline enterprises, most Chinese factories, especially in high-end manufacturing, are still far from achieving "flexibility."
In the context of labor shortages, low efficiency, and high costs posing obstacles, Chutian's collaboration with Tongtianxiao software has taken a proactive step towards achieving digital transformation in internal logistics, not only swiftly responding to production plans but also integrating the overall inventory system for unified and refined management across multiple warehouses. In the realm of high-end pharmaceutical equipment, Chutian's path of transformation and rise can be seen as a typical example of China's manufacturing industry upgrading and transformation.
Share
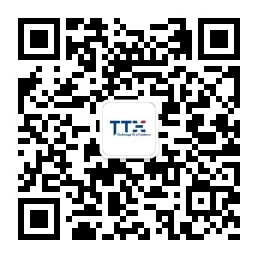
Follow TXX Public
随时掌握企业数字化供应链相关的最新洞察、业界动态,获取供应链科技领域的深度报告和行业白皮书