-
Retail/Distribution
-
E-commerce
-
Fashion
-
Order Management System
-
Warehouse Management System
he footwear giant ECCO collaborates with TTX to achieve unified inventory management
TTX provided ECCO with an OFS solution, helping them achieve unified inventory management across all channels.
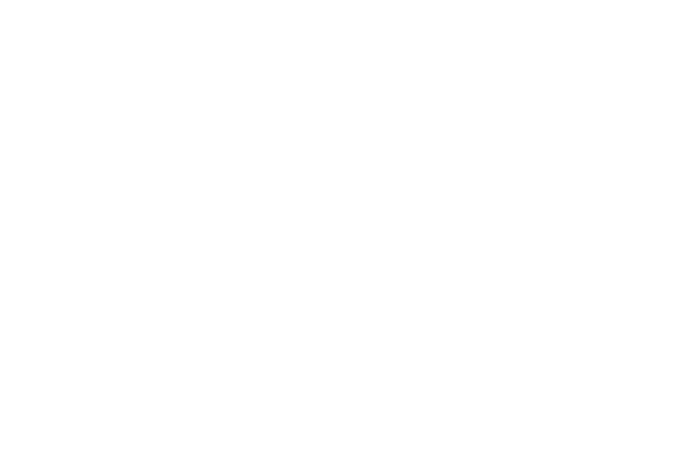
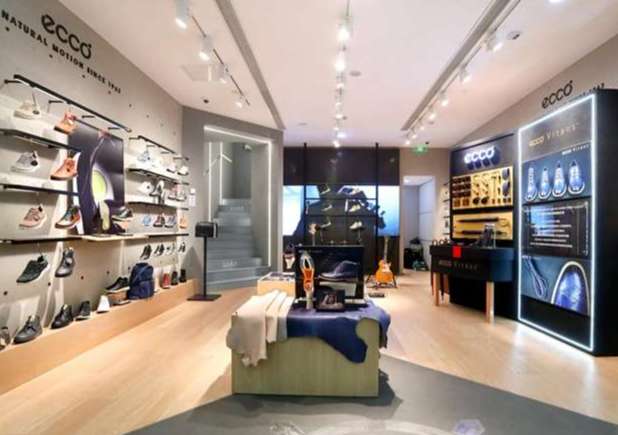
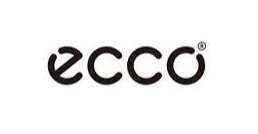
Before the launch of TTX's Order Fulfillment System (OFS), ECCO's 2C and 2B businesses operated under separate fulfillment systems, with orders and inventory data completely disconnected. Any inventory reallocations relied solely on offline manual communication. TTX was fortunate to participate in ECCO's digital supply chain transformation by providing an OFS solution, which enabled ECCO to achieve integrated inventory management across all channels.
On one hand, TTX's Order Fulfillment System (OFS) integrates with the WMS (Warehouse Management System) of three major downstream physical warehouses, consolidating their previously independent inventory management systems into OFS for logical inventory allocation.
OFS categorizes inventory into actual and logical stocks, aligned with WMS inventory processing nodes. Business personnel can operate and view accurate inventory in real time within OFS. The system features comprehensive inventory reconciliation capabilities, allowing rapid reconciliation of inventory discrepancies via interface connectivity, ensuring high-precision inventory management.
OFS also automatically consolidates 2C and 2B inventories daily and proportionally allocates them to meet next-day business requirements.
In ECCO's original business scenarios, various channel orders corresponded to different inventories. Post OFS implementation, orders are matched to specific inventory rather than total warehouse stocks. This often results in instances where a product may appear out of stock in one inventory despite availability in the warehouse. To address such issues, TTX introduced inventory slicing in OFS: when the system indicates insufficient channel inventory, ECCO can adjust inventory ratios across channels by warehouse or SKU within the system, preventing scenarios where warehouses have stock but orders cannot be fulfilled, thereby improving order fulfillment rates.
On the other hand, OFS has also completed integration with the customer's existing upstream systems such as OMS (Order Management System), POS (Point of Sale), and the global business system SAP, consolidating all dispersed fulfillment business orders into a centralized platform for order fulfillment management.
OFS automates the processing of various business documents, uniformly categorizing different types of documents. When outputting to WMS, only two types of documents—outbound and inbound orders—are used, enabling WMS to swiftly handle shipping and receiving tasks.
Additionally, OFS has automated order management. Customers can set up load planning for all sales and inventory business documents within the system, allowing for automated execution and enhancing operational efficiency.
During major promotional periods, if To C warehouse inventory and efficiency cannot meet order demands, TTX's OFS enables ECCO to directly supply To C orders using To B inventory through a unified inventory system. This significantly enhances the flexibility of the supply chain.
Furthermore, OFS has integrated its internal backbone system SAP, ensuring synchronization between business and finance and achieving seamless closed-loop management.
By directly interfacing with the SAP system, OFS has streamlined the import information flow for customer overseas business, enabling closed-loop management of overseas factory reservation orders, shipping vessel numbers, document numbers, container counts, and other information. It also assumes responsibility for managing part of the overseas business's inventory in and out processes.
OFS consolidates sales data from various platforms, automatically conducts detailed data verification on a per-order basis, categorizes exception data for financial review, and interfaces with customer SAP systems to synchronize verified data, thereby enhancing the precision and speed of customer verification tasks.
TTX project manager Ding Changlin mentioned, "ECCO's business requirements are quite unique. Each link of its supply chain already has independent operational systems. It was quite challenging to achieve unified inventory management on the basis of existing systems. In this situation, it was difficult for us to directly recommend a basic, generic system for client use. We had to customize the development of the system according to the client's business characteristics. This placed high demands on the system's flexibility, scalability, and future development. Fortunately, we successfully withstood the pressure of business requirements and completed this project flawlessly according to the client's specifications."
It is worth noting that TTX also collaborated with DHL Supply Chain to provide WMS solutions for multiple domestic warehouses of ECCO, facilitating the integration of various automated devices and achieving automated and intelligent management.
Share
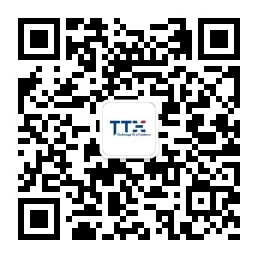
Follow TXX Public
随时掌握企业数字化供应链相关的最新洞察、业界动态,获取供应链科技领域的深度报告和行业白皮书
More Customer Cases
Related Products
-
Order Management System
As the core system of digitalized supply chain, OMS can autonomously implements optimal fulfillment strategies to enhance efficiency and reduce costs.
Learn More
-
Warehouse Management System
A versatile WMS designed to seamlessly address the most intricate warehousing management requirements.
Learn More