ITとOTの統合:スマート製造の核心思想
-
2024-09-14
導入: 今日の急速に変化するビジネス環境において、製造業は前例のない挑戦と機会に直面しています。デジタル化転換はもはや選択肢ではなく、生存のための必須条件となっています。この変革の中で、情報技術(IT)と運用技術(OT)の統合がスマート製造を推進する鍵となっています。本記事では、この統合がどのように製造業の未来を再構築するか、そして企業がこの変革によってもたらされる挑戦にどのように対応するかについて詳しく探ります。
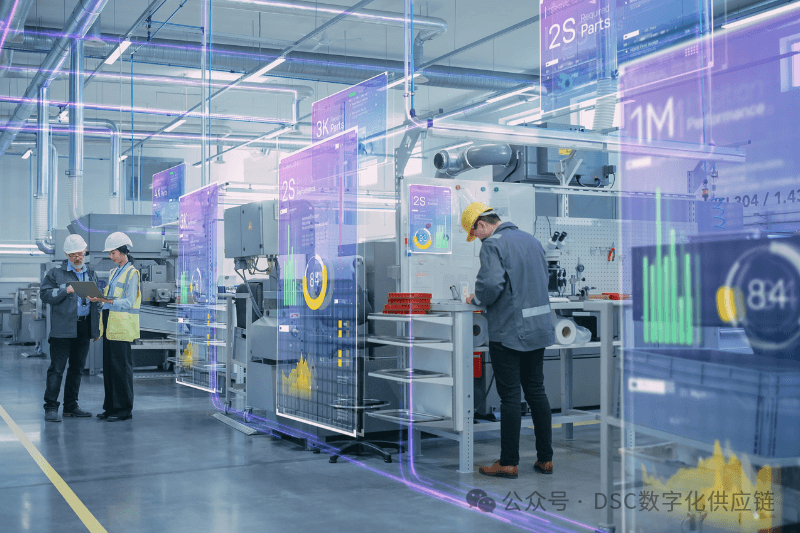
想像してみてください。現代のスマートファクトリーでは、生産ライン上のすべての設備が中央制御システムとリアルタイムで対話しています。機械がわずかな性能の偏差を検出すると、すぐに自らのパラメーターを調整し、この情報を生産ネットワーク全体に伝達します。同時に、サプライチェーン管理システムはこれらのリアルタイムデータに基づいて原材料の注文や生産計画を調整しています。これが情報技術(IT)と運用技術(OT)の統合による変革です。
従来、ITとOTは平行する世界でした。ITは主に企業の情報システム(ERP、CRMなど)を担当し、データ処理と業務プロセス管理に焦点を当てていました。一方、OTは物理的な設備とプロセスの監視と制御を担当し、生産の安定性と効率性を確保していました。これらの分野は長らく独立しており、情報の孤島が形成され、企業の全体的なデジタルトランスフォーメーションの進展を妨げていました。
しかし、インダストリー4.0の到来により、両者の統合が避けられない状況になっています。Flexwareのチーフアーキテクト、Brent Maringerが指摘するように、「新しいプラットフォーム技術が、誰が何を所有し、なぜ所有するのかを再考させている。」この統合は単なる技術の統合ではなく、思考方式の革新でもあります。ITとOTの統合は製造業に前例のない機会をもたらします。
まず、端から端までの可視化と制御が実現されます。原材料の調達から完成品の納品まで、すべてのプロセスがリアルタイムで監視・最適化されます。この全体的な視点により、企業は市場の変化に迅速に対応し、生産の柔軟性を高めることができます。次に、統合は予知保全の進展を促進します。ITシステムのデータ分析能力とOTシステムのリアルタイム監視データを組み合わせることで、企業は設備故障を正確に予測し、予期しないダウンタイムを大幅に削減し、設備の利用率を向上させることができます。ACEの専門家、Craig Eganが強調するように、「事実はデータより重要です。」ここでの「事実」とは、単なる原始データではなく、分析され、文脈化された価値ある情報を指します。
最後に、ITとOTの統合は革新の新たな扉を開きます。例えば、デジタルツイン技術の適用により、企業は仮想環境で生産プロセスをシミュレーション・最適化し、製品開発サイクルを大幅に短縮し、試行錯誤のコストを削減できます。しかし、この統合には課題もあります。「ITとOT技術の進化の道筋は異なります。」この違いは技術面だけでなく、文化や思考方式にも現れます。IT部門は迅速な反復と頻繁な更新に慣れている一方、OT部門は安定性と信頼性を重視しています。生産の安定性を保証しながら革新を推進することが企業の重要な課題となります。
技術的視点:データの孤島を打破し、統一情報モデルを構築する
ITとOTの統合の過程で、核心的な課題はデータの孤島を打破し、統一された情報モデルを構築することです。これは単なる技術的問題ではなく、データの収集、保存、利用方法を根本的に再考するシステム的な挑戦です。
従来の製造環境では、データは通常、さまざまな異なるシステムに分散して保存されています。生産ライン上の設備は独自の通信プロトコルを使用する一方、企業資源計画(ERP)システムはまったく異なるデータ構造を使用します。この分散化により、データが断片化し、企業が全体的なビジネス洞察を得ることが難しくなります。
Jonathan WiseはITとOTのデータモデルの根本的な違いを深く指摘しています。「OT技術の情報モデルは通常、PLCラベルや履歴データベースラベルなどのキー・バリューに基づいています。一方、IT技術はオブジェクトモデルに基づき、クラス、オブジェクト、およびそれらの関係を前提としています。」この違いは単なる技術的なものではなく、二つの領域の全く異なる思考方式を反映しています。
この問題を解決するために、多くの企業は統一命名空間(UNS)の構築を試みています。UNSの目的は、すべてのデータポイントに統一された識別子とアクセス方法を提供することで、データがITシステムからOTシステムに至るまで対応できるようにすることです。しかし、Craig Eganが警告するように、「統一命名空間のゴミは依然としてゴミです。」つまり、基盤となるデータの質が悪ければ、単に命名を統一しても根本的な問題は解決されません。
では、正しい方法とは何でしょうか?その答えは、現代的でITに優しいプラットフォーム層を構築することです。このプラットフォームは以下の重要な特性を持つ必要があります。
まず、それは豊富な情報モデルをサポートする必要があります。このモデルは、さまざまなデータポイントを表現するだけでなく、それらの間の複雑な関係も記述できなければなりません。例えば、生産注文は単なる数字の列ではなく、特定の顧客、製品仕様、生産設備などと密接に関連しています。これらの関係を捉え、表現できるプラットフォームがあれば、高度な分析や意思決定支援の基盤を提供できます。
次に、このプラットフォームは強力なデータ統合能力を備えている必要があります。これは、従来のPLCコントローラーから最新のIoTデバイスに至るまで、さまざまなITおよびOTシステムをシームレスに接続できる必要があります。この統合は単なるデータの移動ではなく、異なるシステムのデータ意味を理解し、変換することが求められます。
第三に、プラットフォームは柔軟なAPIおよびサービスインターフェースを提供すべきです。これにより、開発者はシンプルなデータ可視化ダッシュボードから複雑な人工知能モデルまで、さまざまなアプリケーションを簡単に構築できます。Brent Maringerが言うように、「技術のための技術ではなく、実際の問題を解決するために。」柔軟なインターフェースは実際の問題解決の鍵となります。
最後に、このプラットフォームは強力なセキュリティメカニズムを内蔵している必要があります。ITとOTシステムの統合に伴い、ネットワークセキュリティはこれまで以上に重要です。プラットフォームは、センシティブなデータが未承認のアクセスを受けないように、細かいアクセス制御を実施する必要があります。このようなプラットフォームを構築することは簡単ではありませんが、その潜在的なリターンは大きいです。成功した例として、ある大手自動車メーカーが統一データプラットフォームを構築し、生産ライン、サプライチェーン、カスタマーサービスからのデータを統合しました。これにより、彼らは前例のない端から端までの可視化を実現しました。例えば、特定のバッチの原材料が最終製品の品質にどのように影響するかを追跡し、潜在的な顧客クレームを予測することができます。
しかし、技術だけが全てではありません。Jonathan Wiseが強調するように、「情報モデリングという難しい部分を飛ばすことはできません。」企業は自分たちのデータを理解し、適切なモデルと標準を定義するために大量の時間とリソースを投入する必要があります。これは一度限りの作業ではなく、継続的なプロセスであり、ITとOTのチームの密接な協力が必要です。
この過程で企業は様々な課題に直面する可能性があります。例えば、歴史的なレガシーシステムをどう扱うか、データ品質を保ちながら生産効率に影響を与えないようにするか、標準化と柔軟性のバランスをどう取るかなどです。これらは慎重に考慮すべき問題です。
効果的な戦略は、段階的なアプローチを採用することです。小規模な試行プロジェクトから始め、徐々に範囲を拡大することで、リスクを低減し、組織が学び、調整する時間を確保できます。成功したIT-OT統合を実施した製造業のCIOが言うように、「最初のプロジェクトは完璧ではありませんでしたが、それが次のプロジェクトでより良くする方法を教えてくれました。」
総じて、統一された情報モデルとデータプラットフォームの構築はIT-OT統合の基盤です。これによりデータの孤島を打破し、将来の革新の基礎を築くことができます。この転換を成功させた企業は、スマート製造の時代で先行することができるでしょう。
組織変革:部門間協力と人材育成
ITとOTの融合が進む過程で、技術の重要性は確かに大きいですが、実際の課題は人と組織にあります。Craig Eganが強調するように、「これは単なる技術的な問題ではなく、文化的な問題でもあります。」ITとOTの融合を成功させるためには、従来の部門間の壁を打破し、新たな人材を育成し、組織文化を再構築する必要があります。
まず、IT部門と運用部門の壁を打破することが重要です。 長年にわたり、これらの部門はそれぞれ独自の運営を行い、対立の感情すら存在していました。IT部門は運用部門が現代技術の重要性を理解していないと感じ、運用部門はIT部門の解決策が現実離れしていると感じることがありました。Brent Maringerが述べるように、「過去には『私たち対彼ら』という心態がよく見られました。」この状況を変えるためには、リーダーシップの姿勢と行動が重要です。一部の成功した企業は以下の戦略を採用しました:
部門横断の作業グループを設立する:これらの作業グループはIT部門と運用部門のメンバーで構成され、特定の統合プロジェクトを推進します。共同作業を通じて、双方は相手のニーズと課題をよりよく理解できます。
ローテーションプログラム:IT担当者が工場の現場で一定期間働き、運用担当者がITプロジェクトに参加することを促進します。このような直接的な体験は相互理解を大いに深めます。
共通のKPIを設定する:部門間の重要なパフォーマンス指標を設定し、IT部門と運用部門が共通の目標に向けて努力するよう奨励します。
上層部の支援:企業の上層部が統合を明確に支持し、リソースの配分や意思決定においてそれを反映させる必要があります。
次に、クロスディシプリナリーな人材の育成が重要な課題となります。 Jonathan Wiseが指摘するように、「IT担当者はOTを理解し、OT担当者はITスキルを身につける必要があります。」このようなクロスディシプリナリーな知識は、技術の統合を助けるだけでなく、より良いコミュニケーションと協力を促進します。
一部の先進企業はすでにこの方向で行動を起こしています。たとえば、ある大手製造業者は「デジタルエンジニア」という新たな職種を設立しました。これらのエンジニアは伝統的な製造技術とデータ分析・ソフトウェア開発の両方に精通しており、ITとOTの世界を結ぶ橋渡し役を果たしています。別の企業は地域の大学と協力して、スマート製造に特化したコースを開設し、将来のクロスディシプリナリーな人材を育成しています。
組織文化の再構築においては、企業のリーダーが模範を示し、部門間協力の価値を示す必要があります。 たとえば、ゼネラル・エレクトリックの元CEOジェフ・イメルトは、デジタル化転換プロジェクトに自ら関与し、全社に変革の緊急性を伝えました。このようなトップダウンの変革は、深遠な影響をもたらすことが多いです。
しかし、文化の変革は一朝一夕には実現しません。製造業の幹部が言うように、「技術の変革には数か月かかるかもしれませんが、人の考え方の変革には数年かかるかもしれません。」したがって、企業は忍耐力を持ち、リソースを継続的に投入し、さまざまな方法で新しい文化理念を強化する必要があります。
たとえば、シーメンスはデジタル工場で「デジタルアンバサダー」プログラムを導入しました。これらのアンバサダーは異なる部門からの社員で、専門のトレーニングを受け、日常業務の中でデジタル化の実践を広める役割を果たしています。この方法により、シーメンスはデジタル文化を組織の隅々に浸透させることに成功しました。
もう一つ注目すべきトレンドは「シビルデベロッパー」の台頭です。ローコードやノーコードプラットフォームの普及により、ますます多くの非IT担当者がソフトウェア開発に参加するようになっています。これにより、ITリソースの圧力が軽減され、ビジネスと技術の深い融合が促進されます。ただし、イノベーションを奨励しつつシステムの安定性を維持するバランスを見つけることが管理層の新たな課題となります。
人材育成においては、技術スキルだけでなく、ソフトスキルの重要性も高まっています。 コミュニケーション能力、問題解決能力、チーム協力能力などは、IT-OT融合の環境では特に重要です。先進的な企業はこれらのソフトスキルを社員のトレーニングと評価体系に組み込むようになっています。
最後に、変革管理の重要性に触れておきましょう。 IT-OT融合はしばしば作業フローや役割の大規模な調整を伴い、これが従業員の不安や抵抗感を引き起こすことがあります。効果的な変革管理戦略、すなわち明確なコミュニケーション、十分なトレーニング、合理的なインセンティブメカニズムが変革をスムーズに進めるための鍵となります。Craig Eganが強調するように、「これは旅であり、短距離走ではありません。」企業は長期的な視点を持ち、持続的に投資することで、ITとOTの深い融合を実現し、スマート製造の全潜在能力を引き出すことができます。
実施の道筋:段階的に進め、実効性を重視する
ITとOTの統合における技術的および組織的な課題を検討した後、最も重要な問題に直面しています。それは、どのようにこの変革を実際に実行するかということです。実践からわかることは、成功している企業は、技術の先進性を盲目的に追求するのではなく、実際の効果に重点を置き、段階的なアプローチを取ることが多いということです。
まず、小規模な試験プロジェクトから始めるのは賢明な選択です。Brent Maringerが推奨するように、「大きく考え、小さく始め、速く行動する」ことが重要です。慎重に選ばれた試験プロジェクトは、リスクの少ない環境で新しい技術と作業方式をテストし、貴重な経験を得るのに役立ちます。
例えば、ボッシュはドイツの工場で予知保全の小規模試験プロジェクトを開始しました。彼らは重要な生産ラインを選び、追加のセンサーを設置し、簡単な分析モデルを開発しました。このプロジェクトは予知保全の価値を証明するだけでなく、より大規模な導入時に直面する可能性のある課題を特定するのにも役立ちました。試験プロジェクトを選ぶ際には、企業は以下の要素を考慮する必要があります:
- 価値の潜在性:プロジェクトは明確なビジネス問題を解決し、測定可能な価値をもたらすべきです。
- 可視性:組織内部で一定の影響力を持つプロジェクトを選び、成功後により容易に展開できるようにします。
- 複雑性:プロジェクトは概念を検証するのに十分な複雑さを持ちつつ、管理が難しいほどに大きすぎないようにします。
- 部門間性:理想的な試験プロジェクトは複数の部門を含み、新しい協力モデルをテストするべきです。
次に、企業はデータ量を盲目的に追求するのではなく、情報モデルとデータ品質に高度な注意を払う必要があります。Jonathan Wiseが警告するように、「情報モデリングの困難な部分を飛ばすことはできません。」大規模なデータ収集を開始する前に、データの用途を明確にし、明確なデータ標準とガバナンスプロセスを確立する必要があります。
一例として、大手自動車部品メーカーの反面教師があります。彼らは工場に数千個のセンサーを設置し、膨大なデータを収集しました。しかし、明確なデータモデルと分析フレームワークが欠如していたため、これらのデータの多くは「データの墓場」に過ぎず、実際の価値を生むことはありませんでした。それに対して、別のメーカーはより慎重なアプローチを取りました。彼らは最初に主要なパフォーマンス指標(KPI)を定義し、その後、必要なデータをターゲットを絞って収集・分析しました。この方法はコストを節約し、データの実際の利用可能性を確保しました。
技術選択に関して、企業は「技術崇拝」の罠に警戒する必要があります。Craig Eganが述べるように、「技術が20年の悪習慣を解決するとは限りません。うまくいかなければ、状況がさらに悪化する可能性があります。」技術パートナーとソリューションを選ぶ際には、以下の点に注目すべきです:
- オープン性と相互運用性:既存のシステムとシームレスに統合できるソリューションを選び、新しいデータサイロを作らないようにします。
- 拡張性:ソリューションは企業のニーズの成長に応じて拡張できるべきです。
- ユーザーフレンドリー性:異なるスキルレベルのユーザーを考慮し、ソリューションは使いやすく、メンテナンスしやすいものでなければなりません。
- 総所有コスト:初期投資だけでなく、長期的なメンテナンスとアップグレードコストも考慮に入れるべきです。
実施の過程では、継続的なトレーニングとサポートが重要です。IT-OT統合は複雑な技術とプロセスの変化を伴うため、従業員は新しい作業方式に適応し習得するための時間が必要です。一部の企業は「トレーナーによるトレーニング」モデルを採用し、まず内部の専門家を育成し、その後その専門家がさらに多くの従業員をトレーニングします。この方法はコスト効率が高いだけでなく、内部の知識伝承メカニズムを構築するのにも役立ちます。
もう一つの重要な点は、適切な測定基準を確立することです。管理の巨星ピーター・ドラッカーが言ったように、「測定できなければ管理できません。」企業は包括的なKPIシステムを構築する必要があり、これには伝統的な生産指標だけでなく、デジタルトランスフォーメーション特有の指標(データ品質、システム統合度、デジタルスキル習得度など)も含むべきです。これらの指標は定期的にレビューし、更新することで、常に企業の戦略目標に一致させる必要があります。
最後に、企業はIT-OT統合が一度限りのプロジェクトではなく、継続的なプロセスであることを認識する必要があります。技術は進化し続け、ビジネスのニーズも変化し続けるため、企業は継続的な改善の文化を築く必要があります。これには定期的な技術評価、継続的な従業員スキルの向上、外部パートナーとの密接な協力が含まれる可能性があります。
良い例としては、シーメンスのアンベルク工場の実践があります。彼らは「デジタルツイン」方法を採用し、物理的な工場だけでなく、全生産プロセスのデジタルコピーを作成しました。これにより、仮想環境で新しい生産計画をテストし、実際の実施のリスクとコストを大幅に削減することができました。さらに重要なのは、彼らがこの方法を継続的なプロセスと見なし、実際の生産データに基づいてデジタルモデルを更新・最適化し続けていることです。
要約すると、IT-OT統合を成功裏に実施するには、戦略的な視点、技術的な専門知識、そして組織的な知恵の結合が必要です。企業は短期的な利益と長期的な変革をバランスさせ、試行錯誤の中で学び、実践の中で改善を図る必要があります。デジタルトランスフォーメーションに成功したCEOが言うように、「これは目的地ではなく、旅路です。重要なのは正しい方向を保ち、途中で学び続け調整することです。」
===========
この記事の内容は、Public Account-DSC Digital Supply Chain から転載されています。この記事は著者の意見を表明したものにすぎません。ご提案やご質問がございましたら、私までご連絡ください。
DSC(デジタルサプライチェーン)は、国内一流のデジタル化とサプライチェーンの専門家を集め、大規模サプライチェーン分野の専門的問題や最先端のホットスポットについて議論し、デジタル分野におけるサプライチェーンの発展の方向性を探ることを目的としています。
END

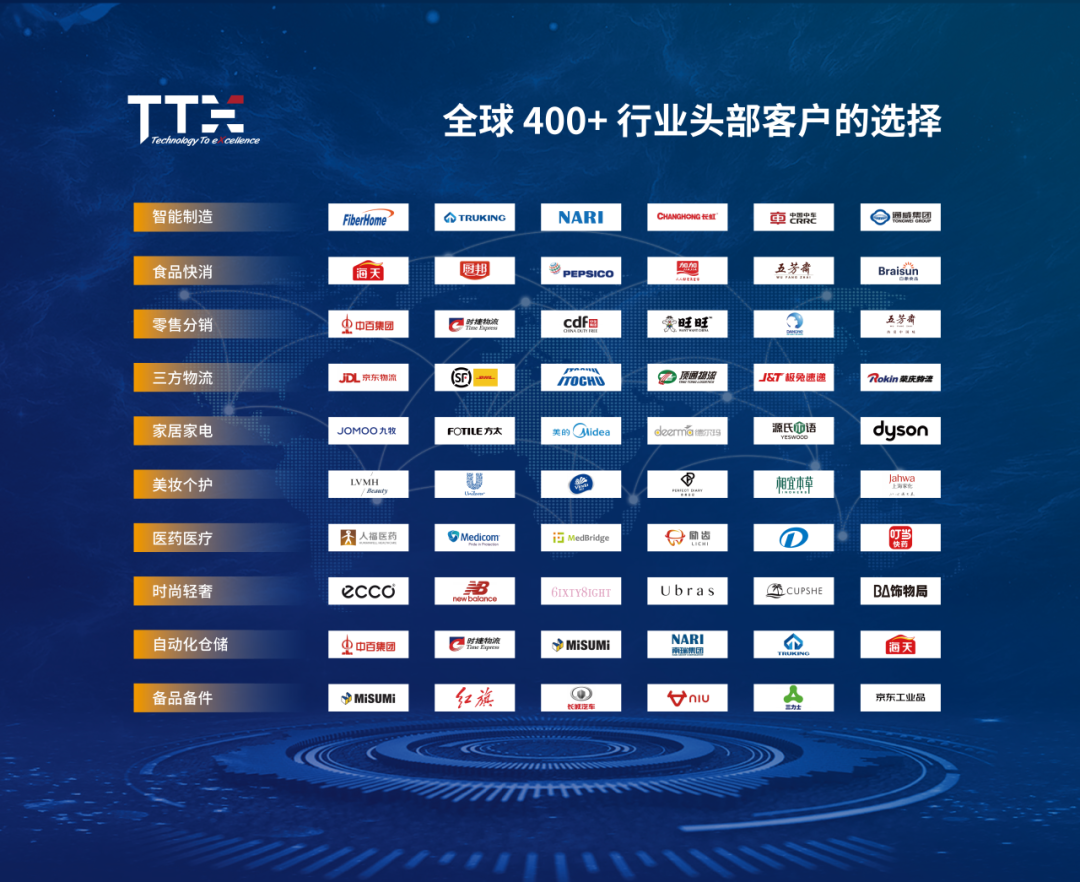